Research Projects
COM3
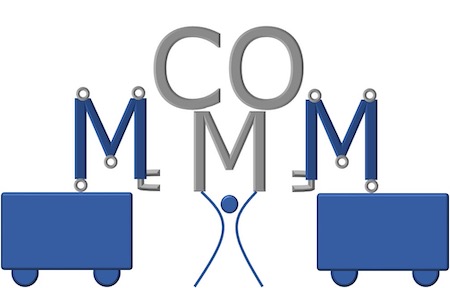
Project Title: COoperative Mobile Manipulators for Manufacturing (COM3)
Project funded by: Italian Ministry of University and Research - Research Program of National Interest (PRIN) 2022 - Project no. 2022ZLYBF5
Programmed duration: 24 months (2022-2024)
Scientific responsible: Fabrizio Caccavale
Objectives: Cooperative robotics can be identified as a key technology to support agile manufacturing
and the Industry 4.0 paradigm. In order to fully exploit the potential of cooperative robotics in the domain of advanced production
systems, especially in terms of agility and adaptability, further steps forward in robot-robot cooperation are needed.
To enhance layout flexibility and optimize production, the use of mobile manipulators in production lines needs to be expanded.
These should be capable of performing cooperative manipulation tasks, such as transporting large/heavy parts or assembly tasks,
potentially in collaboration with humans to leverage their cognitive abilities in handling unexpected situations or in executing complex manipulation tasks.
The collaboration between humans and robots needs to expand from single-robot interactions to multi-robot systems, which presents more complexity and
can increase cognitive stress for humans due to less predictable robotic behavior.
A shift towards bidirectional communication is essential, where robots inform human operators about their state and planned actions.
In the framework of the COM3 project, the above identified research challenges will be tackled by addressing the following research 3 objectives:
- 1. Development of advanced approaches to cooperative mobile manipulation.
- 2. Development of approaches to bidirectional human-robot communication and interaction for collaborative robotic systems composed of multiple mobile manipulators.
- 3. Experimental demonstration of the capabilities of cooperative mobile manipulators in industrially relevant use cases.
An additional objective is to implement a suitable dissemination and communication strategy.
MELODY
Project Title: Multi robot collaborativE manipuLation suppOrting DisassemblY tasks (MELODY)
Project funded by: Italian Ministry of University and Research - Research Program of National Interest (PRIN) 2022 - Project no. P2022XALNS
Programmed duration: 24 months (2022-2024)
Scientific responsible: Francesco Pierri
Objectives: MELODY aims at:
Developing a framework to sustain circularity while anticipating process adaptation to flexible recovery. In this
perspective, MELODY aims at defining solutions to assess the health status of the product’s components in order to
configure disassembly tasks. Assessment of the component’s remaining useful life is important per se since it consists of a
predictable tool useful in defining status of the product (repair, scrap or reuse) as well as of its individual components (reuse,
regenerate or scrap). In the disassembly task context, to predict and assess product status will help the scheduling of human and
robot activities and make their interaction more efficient.
Developing collaborative strategies for bi-directional interaction between humans and a system composed by
multiple mobile manipulators, based on the reciprocal learning paradigm with the major aim to provide benefits to humans,
robots and process. MELODY requires usage of I4.0 enabling technologies to bring necessary information to help both humans and
robots to actively learn during the process and adjust their behavior.
Developing novel approaches to coordination and cooperation of mobile manipulators in recovery and Closed Loop
Supply Chain. Decentralized control strategies will be investigated, over different inner requirements, since they confer flexibility
and sometimes are the only possible approach when the communication with all the robots is impossible, e.g. in the presence of
short-communication-range capabilities.
TECH4YOU
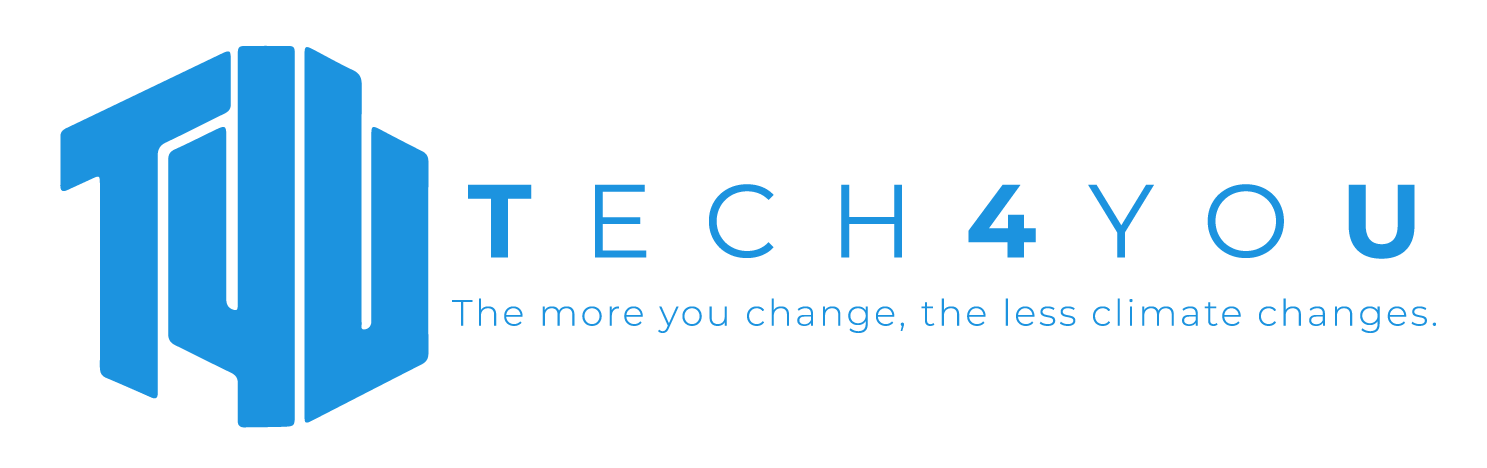
Project Title: TITLE
Project funded by: INSERT
Programmed duration: 36 months (2023-2025)
Local scientific responsible: Ferdinando Mirizzi
Local scientific responsible for Spoke 6: Francesco Pierri
Objectives: INSERTI TEXT
ICOSAF
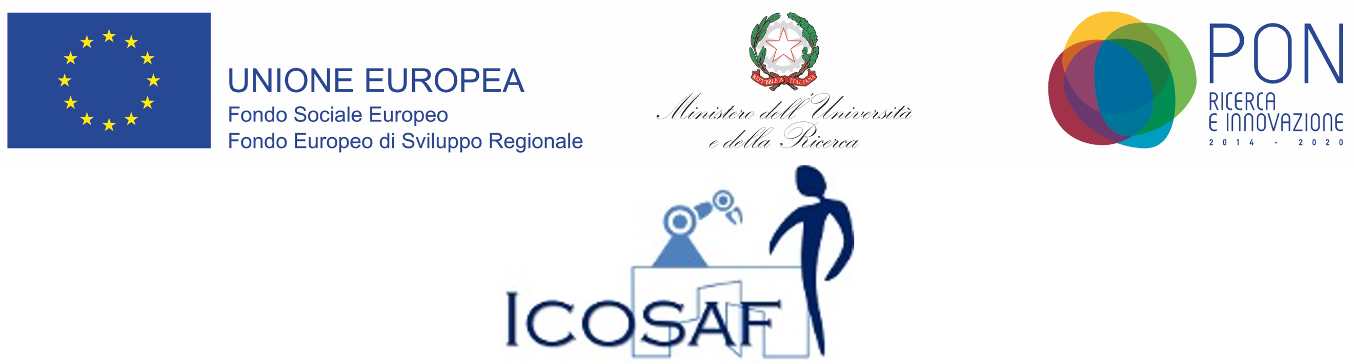
Project Title: Integrated
COllaborative systems for SmArt Factory
Project funded by: Italian Ministry of University
and Research under PON Ricerca e Innovazione 2014-2020 Program -
Project no. ARS01_00861
Programmed duration: 42 months (2018-2022)
Scientific responsible: Fabrizio Caccavale
Objectives: ICOSAF aims to develop and integrate
technologies and solutions for a collaborative factory with a
growing integration of the operator with collaborative automation
systems. Requirements such as flexibility, scalability, modularity
and reconfigurability of production facilities are fundamental in
today0s manufacturing industry. Currently the trend is to fully
automate many operations with the use of appropriate technologies,
but maximum flexibility is always achieved with the use of human
staff that is inherently flexible. By a social point of view,
however arises the need to support operators (with increasing age)
with technologies that reduce the impact of ergonomic fatigue by
increasing the quality and productivity. Therefore the project aims
to facilitate the insertion of human-machine interface technologies
and/or other technologies for greater flexibility and
reconfigurability by improving and developing technologies for a
more efficient functionality from a cooperativity point of view. The
integration into the intelligent factory of cooperative and
autonomous systems that ICOSAF aims for will bring improvements in
terms of productivity, quality, flexibility, ergonomics and work
environment for operators. The main technologies developed within
the project are related to: Cooperative Robotics, Autonomous AGVs,
Distributed maintenance and quality support systems, Advanced
human-machine interfaces, Simulation models and virtual/augmented
reality systems.
PROMPT
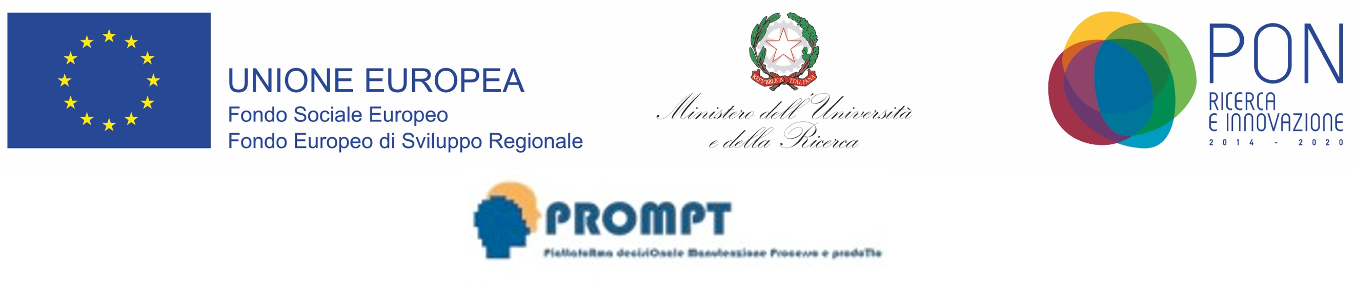
Project Title: PiattafoRma
decisiOnale Manutenzione Processo e prodoTto
Project funded by: Italian Ministry of University
and Research under PON Ricerca e Innovazione 2014-2020 Program -
Project no. ARS01_01046
Programmed duration: 36 months (2018-2021)
Scientific responsible: Fabio Fruggiero
Objectives: PROMPT project (Platform for Resource
Planning and Product Development) aims to develop a software
platform providing a decision support system (DSS) for operators
that will be supported by technology in process management,
industrial planning, and productive choices. Within this project an
open, modular and scalar software platform will be designed and
developed that favors interoperability between devices, capable of
processing the collected information and providing the end-user with
functionality specific to smart manufacturing, including predictive
maintenance with the aid of the digital twin. The development of a
module that helps the user in the maintenance of the plant or a part
of it has become necessary for a twofold reason; on the one hand,
it’s important to use the large amount of data collected from the
platform and to test its consistency, usability with a specific
function, maintenance, which, by its very nature, requires a lot of
up-to-date information. The second reason is that new production
modeling methodologies find extensive applicability not only in the
field of maintenance, and can therefore serve as the basis for other
services enriching the platform. Despite the clear advantage of
studying production flows on a faithful "copy" of the plant, rather
than in the factory operating reality, digital twins represent, in
particular, in the Italian production context, a very rare and
limited reality for companies of niche with particular propensity to
innovation. This is because in addition to being particularly
complex to develop, digital twin requires an appropriate software
infrastructure to capture data, making them available even when they
come from different sources and in different formats; they also need
to use algorithms to analyze and study recovered data, which are
able to transform them into input information into appropriate
control and optimization systems, which in turn can be used as
decision support systems. Information received from predictive
algorithms based on historical data, to suggest or apply solutions.
Therefore their insertion and use within the PROMPT platform is an
innovative feature of the project.
AEROARMS
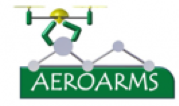
Project Title: AErial RObotics
System integrating multiple ARMS and advanced manipulation
capabilities for inspection and maintenance
Project funded by: European Community under Horizon
2020
Programmed duration: 48 months (2015-2019)
Scientific responsible: Francesco Pierri
Objectives: AEROARMS proposes the development of
the first aerial robotic system with multiple arms and advanced
manipulation capabilities to be applied in industrial inspection and
maintenance (I&M). The project poses complex mechatronics,
control, telemanipulation perception and planning problems.
Particularly, new mechatronic designs and control methods are needed
to implement the aerial robots with several arms for grabbing and
flying operations. Advanced control strategies with force and vision
feedback are also required for manipulation. Also new coordinated
control strategies of the multiple arms and the aerial platforms are
needed. Moreover, new perception methods, with ability to adapt to
changing illumination conditions, are required for accurate local
mapping and localisation in denied GPS industrial environment,
grabbing and manipulation, and integration of sensory data to help
the operation of the crawler. On the other hand, planning is
required to compute the required motions of the aerial robot for
efficient and safe grabbing and manipulation taking into account the
constraints imposed by the aerial robot and the environment,
including motion planning for torque compensation, and for
cooperation with the ground mobile robot. Moreover, reactive
behaviours to increase safety, avoiding collisions with objects in
the environment will be also implemented.
EuRoC
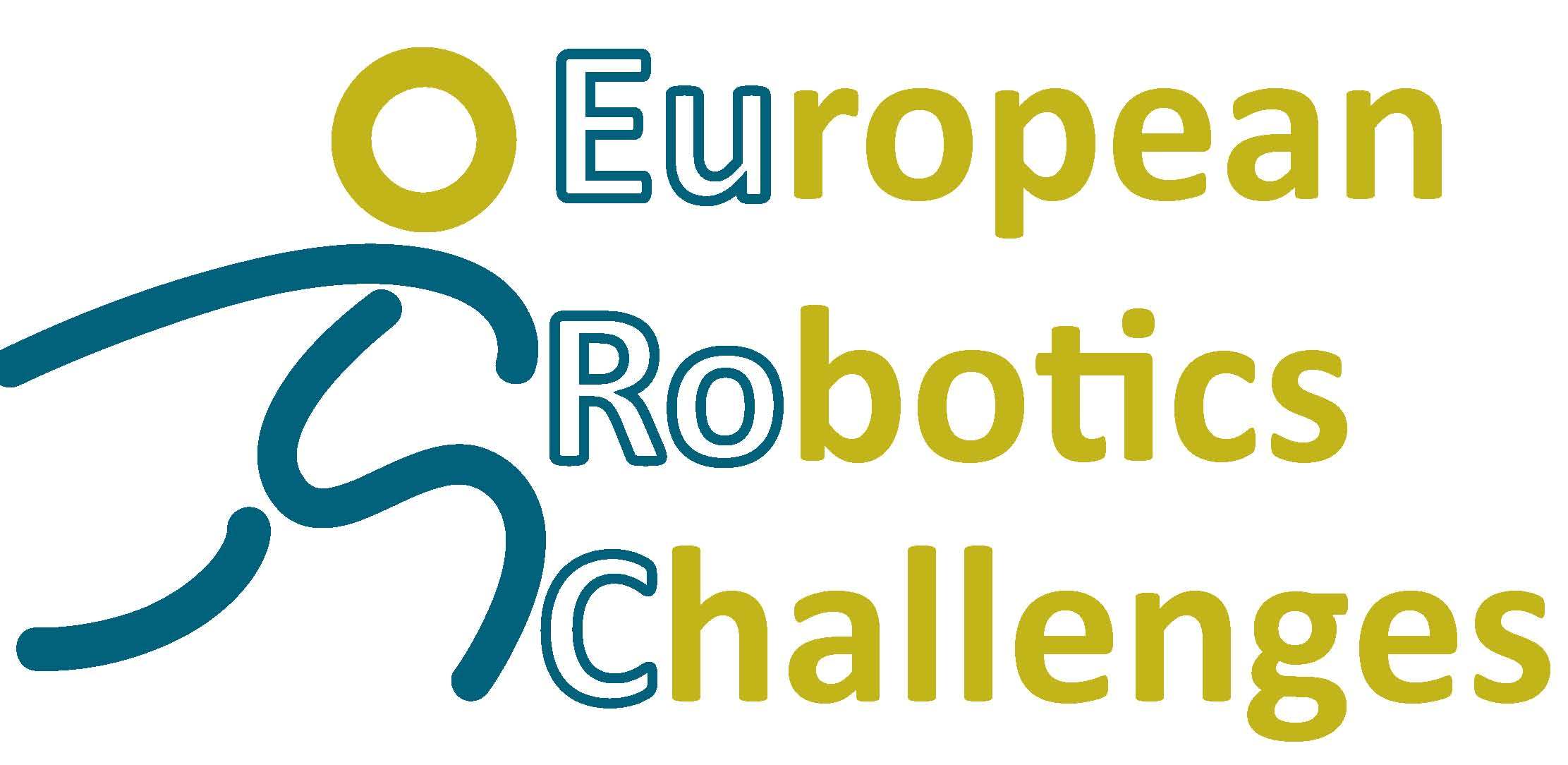
Project Title: European Robotics
Challenges
Project funded by: European Community under FP7
Programmed duration: 54 months (2014-2018)
Scientific responsible: Fabrizio Caccavale
Objectives: The European manufacturing industry
needs competitive solutions to keep global leadership in products
and services. Exploiting synergies across application experts,
technology suppliers, system integrators and service providers will
speed up the process of bringing innovative technologies from
research labs to industrial end-users. As an enabler in this
context, the EuRoC initiative proposes to launch three
industry-relevant challenges: Reconfigurable Interactive
Manufacturing Cell, Shop Floor Logistics and Manipulation, Plant
Servicing and Inspection. It aims at sharpening the focus of
European manufacturing through a number of application experiments,
while adopting an innovative approach which ensures comparative
performance evaluation. Each challenge is launched via an open call
and is structured in 3 stages. 45 Contestants are selected using a
challenge in a simulation environment: the low barrier of entry
allows new players to compete with established robotics teams.
Matching up the best Contestants with industrial end users, 15
Challenger teams are admitted to the second stage, where the typical
team is formed by research experts, technology suppliers, system
integrators, plus end users. Teams are required to benchmark use
cases on standard robotic platforms empowered by this consortium.
After a mid-term evaluation with public competition, the teams
advance to showcasing the use case in a realistic environment. After
an open judging process, 6 Challenge Finalists are admitted to run
pilot experiments in a real environment at end-user sites to
determine the final EuRoC Winner. A number of challenge advisors and
independent experts decide about access to the subsequent stages. A
challenge-based approach with multiple stages of increasing
complexity and financial support for competing teams will level the
playing field for new contestants, attract new developers and new
end users toward customisable robot applications, and provide
sustainable solutions to carry out future challenges.
ARCAS
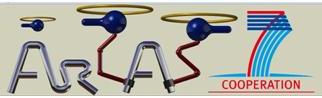
Project Title: Aerial Robotics
Cooperative Assembly System
Project funded by: European Community under FP7
Programmed duration: 48 months (2011-2015)
Scientific responsible: Fabrizio Caccavale
Objectives: The ARCAS project proposes the
development and experimental validation of the first cooperative
free-flying robot system for assembly and structure construction.
The project will pave the way for a large number of applications
including the building of platforms for evacuation of people or
landing aircrafts, the inspection and maintenance of facilities and
the construction of structures in inaccessible sites and in the
space.
PRIN 2009: ROCOCO
Project Title:COoperative and
COllaborative RObotics
Project funded by: Italian Ministry of University
and Research - Research Program of National Interest (PRIN) 2009
Programmed duration: 24 months (2011-2013)
Scientific responsible: Fabrizio Caccavale
(coordinator of local research unit)
Objectives: The project is focused on the
development of control solutions for multiple robotic systems in
tight cooperation, also with human beings, to execute different
task, and the development of supervisory control solutions for a
robotic work-cell, including the cooperative robots, an automatic
warehouse system and other coordinated devices.
ECHORD

Project Title: European Clearing
House for Open Robotics Development
Project funded by: European Community under FP7
Programmed duration: 56 months (2009-2013)
Scientific responsible: Fabrizio Caccavale
Objectives: ECHORD is an innovative framework aimed
at facilitating knowledge advancement and technology transfer
between academia and industry in European robotics. Manufacturers
and research groups have the chance to perform jointly small-size
projects (experiments) which can be rapidly negotiated, funded and
executed.
PRIN 2007: HiFlex
Project Title: Control themes in
hyperflexible robotic workcells
Project funded by: Italian Ministry of University
and Research - Research Program of National Interest (PRIN) 2007
Programmed duration: 24 months (2008-2010)
Scientific responsible: Fabrizio Caccavale
(coordinator of local research unit)
Objectives: The project is aimed at achieving
significant advancements in the field of control of cooperative
systems within hyperflexible robotic work-cells.
An Experimental Setup for Cooperative Robotics based on ROSED
Project Title: Realizzazione di
un’installazione sperimentale per la robotica cooperante basata su
ROSED
Project funded by: ASI (Italian Space Agency)
Programmed duration: 15 months (2007-2009)
Scientific responsible: Fabrizio Caccavale
(national coordinator)
Objectives: ROSED (RObotics SErvicing Demonstrator)
is a dual-arm robotic workcell operating at the Centro di Geodesia
Spaziale (Matera, Italy) of the Italian Space Agency (ASI). The
project is aimed at buliding a PC-based open architecture controller
for ROSED. A Linux-based software environment is the core of the
controller, capable of integrating: two communication links to/from
the manipulators motors drives/jonts sensors, measurements from two
wrist-mounted force/torque sensors, management of the two grippers
mounted at the end effector of each manipulator and of two joysticks
issuing cartesian motion commands. The project team is composed by:
University of Basilicata (coordinator), University of Napoli
Federico II, University of Cassino, University of Roma Tre,
University of Genova.
Development of fault diagnosis systems for aerospace systems, chemical and fusion reactors, and robotic systems
Project Title: Sviluppo di
algoritmi di rilevazione ed isolamento dei guasti con applicazioni a
sistemi aeronautici, reattori chimici, reattori per la fusione
nucleare e sistemi robotici
Project funded by: Fondazione CARICAL
Programmed duration: 24 months (2003-2005)
Scientific responsible: Fabrizio Caccavale
(coordinator of local research unit)