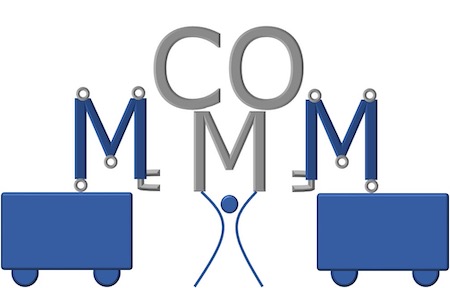
Project Title: COoperative Mobile Manipulators for Manufacturing (COM3)
Research call: PRIN 2022 (D.D. n.104 del 02.02.2022)
Main ERC field: PE - Physical Sciences and Engineering (PE7)
Project funded by: Italian Ministry of University and Research (MUR) - Research Program of National Interest (PRIN) 2022
Project number: 2022ZLYBF5
Programmed duration: 24 months (2022-2024)
Start Date of Activities: 28 September 2023
Expected Completion Date of Activities: 28 September 2025
Scientific coordinator: Fabrizio Caccavale
Units Involved:
- University of Basilicata (scientific coordination of the project), unit head: Prof. Fabrizio Caccavale
- University of Cassino and Southern Lazio, unit head: Prof. Filippo Arrichiello
Total Costs: € 277,069
Total MUR Funding: € 199,851
MUR Contribution to the University of Basilicata: € 99,488
MUR Contribution to the University of Cassino and Southern Lazio: € 100,363
Motivation, challenges and objectives of the project:
Cooperative robotics can be identified as a key technology to support agile manufacturing and the Industry 4.0 paradigm. In order to fully exploit the potential of cooperative robotics in the domain of advanced production systems, especially in terms of agility and adaptability, further steps forward in robot-robot cooperation are needed. Namely:
- In order to improve layout flexibility and achieve production optimization, the adoption of mobile manipulators on production lines must be further spread, where these must be capable of performing cooperative manipulation tasks (e.g., transportation of large/heavy parts on the shop floor or assembly tasks). Such tasks can be executed in collaboration with humans, in order to exploit her/his superior cognitive capabilities to tackle unexpected situations and/or help to execute complex manipulation tasks.
- Thus, collaboration between humans and robots shall be extended to the case where the human operator interacts with multi-robot systems, where the current paradigm is essentially focused on interaction with single-robot systems. However, interaction with multiple robots becomes even more complex for humans, as the behavior of the robotic system becomes less explainable and predictable, affecting ergonomy as well (e.g., by introducing additional cognitive stress). Thus, a fundamental change of paradigm has to be pursued: from human-to-robot unidirectional information flow (e.g., the robot attempts to recognize human intention) to human-robot bidirectional communication, where the robot provides appropriate information on its current state and planned actions to the human operator. For instance, consider a system of cooperative mobile manipulators exploited to handle a large and/or heavy payload. This task can be executed in collaboration with a human operator, which can provide fine adjustments of the trajectory of the object grasped by the multi-manipulator system (e.g., to help parts mating in assembly tasks or provide path adjustments in transportation tasks) by physically interacting with it. On the other hand, when the robotic system deviates from its “nominal” planned trajectory (e.g., to avoid an obstacle detected by the robotic system but not by the human operator), the human should be alerted via appropriate means (e.g., explicit visual/vocal messages).
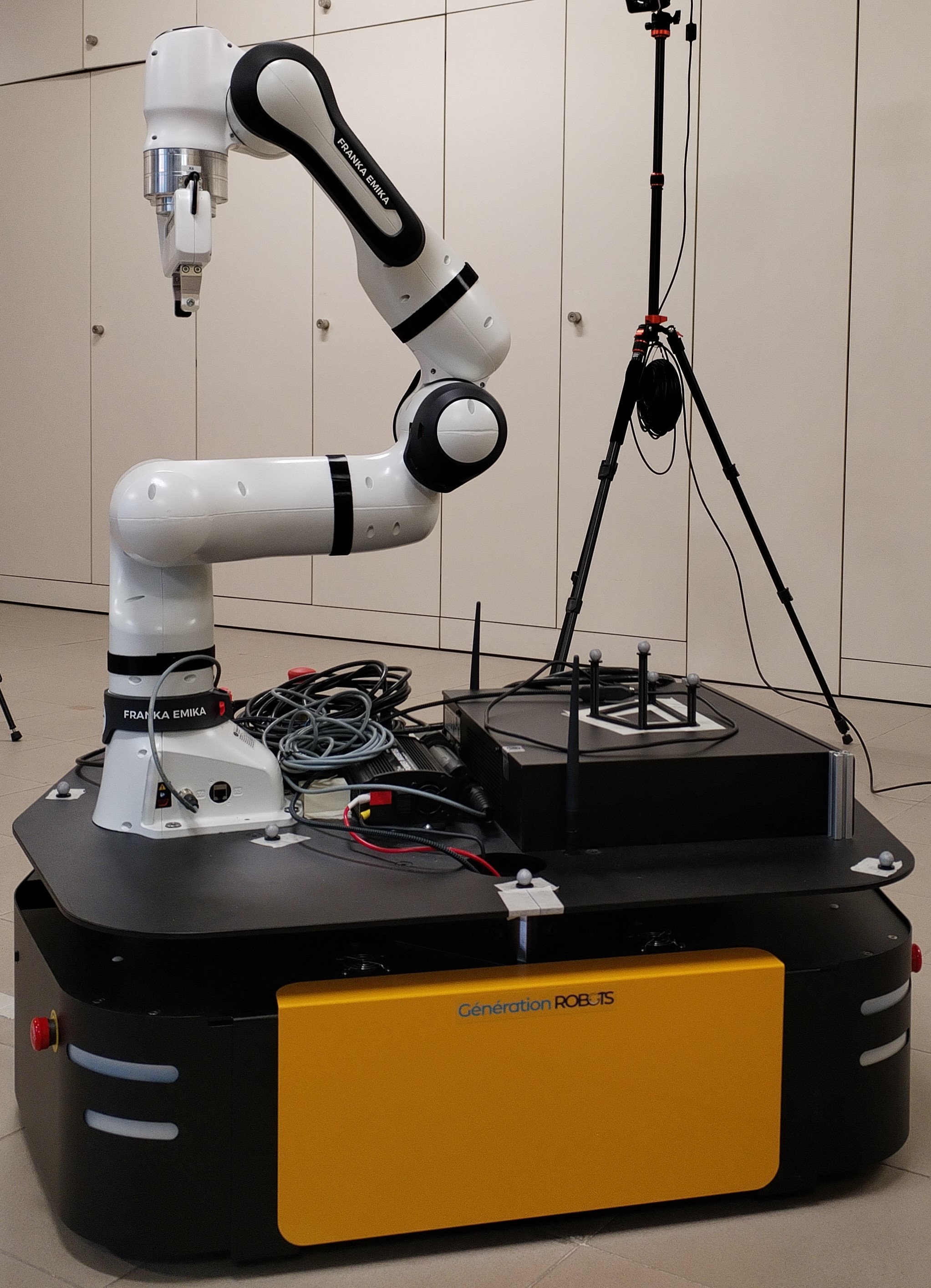
- Cooperative mobile manipulation. In order to confer a proper degree of adaptability and flexibility to cooperative mobile manipulators, advanced estimation/perception capabilities (e.g., visual object detection and estimation of its geometric features, payload parameters), as well as novel distributed control (to maximize flexibility and adaptability) and diagnosis (to improve safety and predictability) methods have to be developed and/or extended to the case of systems composed by multiple mobile manipulators, where redundancy of the whole system shall be exploited as well, to optimize relevant indexes related to the cooperative task, via suitably designed task-priority strategies.
- Human-robot communication and interaction for cooperative mobile manipulators. Natural and flexible collaboration with mobile manipulators requires an advanced interaction framework that enables continuous human-robot communication and ergonomic task adaptation during both physical and cognitive interaction. In this setting, innovative methods for implicit (e.g., exchanged force) and explicit (via AR technologies) bidirectional communication have to be developed and integrated. Although safety of collaborative robotic systems is undoubtedly a relevant issue, in order to keep the project clearly focused and avoid spreading the research effort over an excessively large number of objectives, COM3 will not address it explicitly. Nonetheless, safety requirements will be considered among design parameters of the developed Use Case (UC) and state-of-the-art solutions will be exploited.
- Development of advanced approaches to cooperative mobile manipulation.
- Development of approaches to bidirectional human-robot communication and interaction for collaborative robotic systems composed of multiple mobile manipulators.
- Experimental demonstration of the capabilities of cooperative mobile manipulators in industrially relevant use cases.